Cement Dispersion Technology
The Functions and Roles of Dispersants
When such inorganic particles as cement are mixed with water and stirred vigorously with mechanical force, the particles temporarily disperse in the aqueous solution. However, after a short time, the particles begin to coagulate and coagulations are formed (see Fig. 1).
Generally, the slurry of water and particles rapidly loses fluidity once the particles begin coagulating. This is because the attractive force leading to cohesion (cohesive force) is greater than the kinetic force (from the mechanical stirring action) dispersing the particles; therefore, the particles tend to coagulate. The use of dispersants helps each particle remain separate and dispersed in an aqueous solution by curbing the cohesive force.
Fig. 1 The mechanism of cement dispersion
Generally, dispersants are water-soluble polymers. To obtain maximal effectiveness, these water-soluble polymers must adsorb onto the surface of particles that the user wishes to disperse. Many water-soluble polymers that have been used as dispersants have both hydrophobic and hydrophilic portions. The hydrophobic portion tends to adsorb onto the surface of particle and the latter promotes spread in water phase. Adsorption will largely be affected by the degree of hydrophobic force attracting the polymer to the particle. In the case of dispersants for cement, such agents must be designed with due consideration given to the surface condition of the cement particles, which undergo continually changes after being brought into contact with water. The following describes two ways in which the adsorption of water-soluble polymers onto the surface of cement particles counters the cohesive force of cement particles (see Fig. 2).
Fig. 2 The schematic of the particle structure
- The particles are dispersed due to electrostatic repulsion caused by the formation of a charged layer of adsorbed polymer/material on the surface of each particle.
- The particles are dispersed due to mutual steric repulsion exerted by the layer of adsorbed polymer/material formed on the surface of each particle.
Of these two dispersion mechanisms, (1) is conventionally well-known as the action of concrete dispersants based on melamine sulfonic acid and naphthalenesulfonic acid. On the other hand, the use of (2) has increased quantitatively throughout the market in the last 10 years. It has been applied using polycarboxylic acid-based dispersants and has shown greater effectiveness than agents utilizing electrostatic repulsion when mixing cement with a lower volume of water and a higher particle density.
The Development of Dispersants for Cement
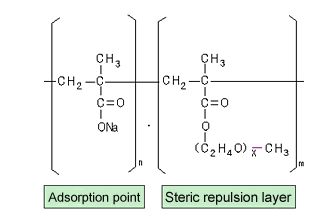
acid-based dispersants
The molecules of the polymer used in polycarboxylic acid-based dispersants comprise a portion that adsorbs onto the surface of cement particles and a portion that displays a steric repulsion effect (see Fig. 3). In designing the optimal formulation for a dispersant with superior effectiveness, we gave due consideration to such factors as (i) molecular mass, (ii) ratio of adsorption point to steric repulsion layer (n/m) and (iii) the bulk and height of the steric repulsion layer (x). In addition, LEOPACK series dispersants incorporate other ingredients to enable a powder formulation. Also incorporated in the series' formulation is another type of polycarboxylic acid-based dispersant with a chemical structure that helps ensure that the dispersion is stable and lasting despite the constantly changing surface condition of the cement particles once they are hydrated.
Application as a Dispersants for Concrete ~ Solubility of Powder Form LEOPACK
Originally, it was thought that the polycarboxylic acid-based dispersants discussed here would be effective as super-plasticizers for concrete. However, when these agents are used in conventional liquid form, specialists were needed during mixing to monitor and control their addition into the mix. With an eye to developing a more user-friendly super-plasticizer, we developed powder formulations packaged in preset volumes.
Fig. 4 The solubility of the powder with particles with an inorganic coating
In the course of the development, the following issues were identified.
- The dispersant must quickly dissolve as it is being mixed into the concrete
- In contrast, the packaging material must not dissolve during storage and transport
After giving due consideration to the abovementioned issues, we instituted the following measures:
- Improved solubility by coating the surface of the powder's particles with certain inorganic matter (see Fig. 4)
- Carboxymethylcellulose is used as the packaging material. This material is selectively soluble at the pH of concrete dispersion liquid (see Fig. 5)
Of course, LEOPACK displays superior water reduction effectiveness and largely reduces slump loss as a super-plasticizer on a level equal to that of high-performance AE water reducing agents. We would be very pleased if you would try easy-to-use and lightweight LEOPACK and experience for yourself its superior fluidity.
Fig. 5 The solubility of the powder with particles with an inorganic coating
Fig. 6 Alkaline-soluble paper and the effect of pH on solubility